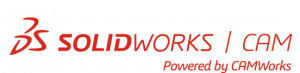

SOLIDWORKS CAM STANDARD
SOLIDWORKS CAM PROFESSIONAL
CAMWORKS STANDARD
CAMWORKS MILLING STANDARD
CAMWORKS TURNING STANDARD
CAMWORKS MILLING PRO
CAMWORKS TURNING PRO
CAMWORKS PREMIUM
CAMWORKS
Bundle
Add-Ons
2.5 osno rezkanje
3 osno rezkanje – stopnja 1*
Cimco Editor/DNC
2.5 osni Volumill
Delo s SOLIDWORKS sestavi
3 osno rezkanje – stopnja 1+*
4/5 osno indeksirno rezkanje
Struženje
Pomožno vreteno (struženje)
Rotacijsko rezkanje
3 osno rezkanje – stopnja 2*
Struženje z gnanimi orodji
3 osno rezkanje – stopnja 3*
Sinhronizator več kanalnih stružnic
Virtual Machine Standard
4 osno rezkanje (dodatek za Milling Pro)
5 osno simultano rezkanje
3 osni Volumill
Virtual Machine Professional
Virtual Machine Premium
Žična EDM erozija**
NestingWorks**
CAMWorks ShopFloor**
PrimeTurning™
CAMWorks pripomočki
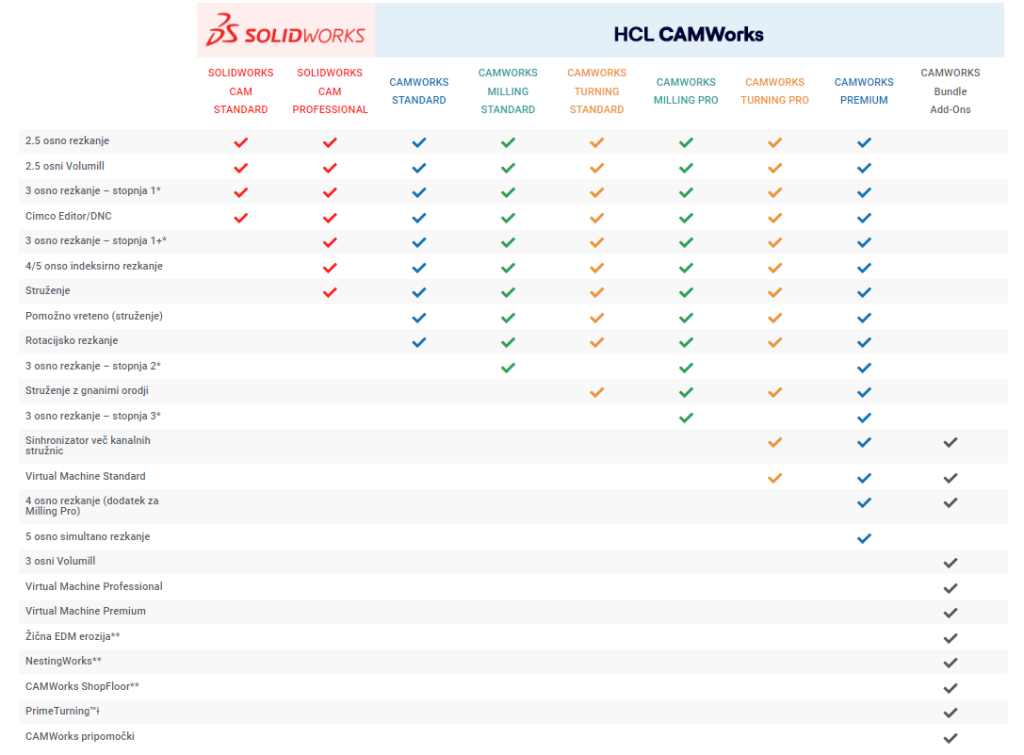
*3 osno rezkanje stopnja 1 vključuje: Area Clear Roughing, Flat Area in Z-Level Finishing
*3 osno rezkanje stopnja 1+ vključuje fukcionalnosti stopnje 1 in dodatno Z-Level inishing with Constant Step-over
*3 Axis Milling Level 2 vključuje funkcije Level 1+ in Pattern Project, Constant Step, Pencil Milling, Curve Project, and Legacy Rough & Finish Mill, Rest Machining za vse 3-osne operacije.
*3 Axis Milling Level 3 vključuje funkcije Level 2 in Undercutting, Fillet Machining, True Surface Machining in Rest Machining za vse 3-osne operacije
** Na voljo tudi kot neodvisni nakupi.
Ɨ PrimeTurning je Sandvik Coromant produkt.